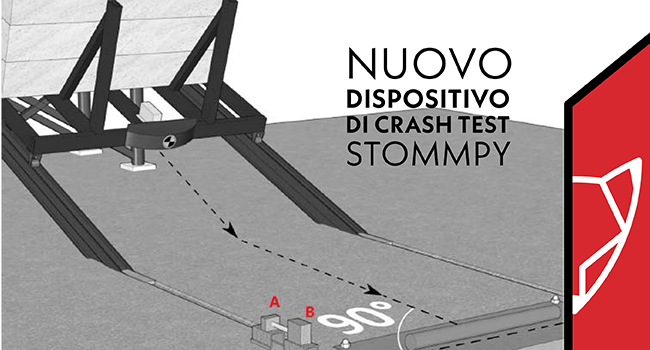
NEW STOMMPY CRASH TEST DEVICE: A unique impact protection testing machine is born from the R&D department
At the end of an important development path that has involved collaboration with numerous players in the safety field, STOMMPY presents its new crash test device for crash protectors, an innovative machine destined to set the line at the European level as well.
The idea of equipping STOMMPY with its own testing system for products dates back to 2018, and was born after a long and fruitful collaboration between the company and a highway barrier testing and certification laboratory.
The first pre-feasibility examination was followed in 2019 by the preparation of project documentation for participation in a Call for Proposals of the Emilia-Romagna Region to support innovative projects in SMEs.
The Region quickly approved the project, recognizing its high degree of innovativeness, especially in view of the fact that it is the first crash test machine, worldwide, that operates in a way that is fully compliant with the requirements of the UNI standards relating to Impact Protections in the Industrial Field; standards that are currently being revised with a view to their next publication, expected in early 2022.
In April 2020, STOMMPY's Research & Development Department was thus able to begin the executive design of the machine, and later its actual construction, which was completed in August 2021.
A MACHINE THAT IS UNIQUE IN THE WORLD IN TERMS OF SHAPE, SENSOR TECHNOLOGY AND INNOVATIVENESS
This is a sled system, an inclined plane on which, to simulate an impact against a protective device, three different mass values - 1500, 4000 and 6000 kg - can be configured, according to the UNI technical specification. The same standard also defines the geometry of the impactor to be used, in order to reproduce the rear outline of a classic forklift.
The machine has been appropriately oversized in its mechanical structure, to be able to safely develop dynamic shocks up to the extraordinary value of 60,000 joules, well beyond the already remarkable value of 50,000 joules of the maximum class of resistance provided for in the UNI technical specification; values of resistance that, however, to date, are not matched in the panorama of shock protections on the market, but which certainly represent the future goals to which STOMMPY aspires to reach.
The system is entirely managed by dedicated software, developed in cooperation with a specialized company according to the specifications and direct supervision of STOMMPY's R&D department. The software controls a large complex of electronic instrumentation and sensing sensors for controlling the release height of the sled - different depending on the impact force to be simulated - and for detecting the effects of impacts on the impact protection to be tested, including a set of video cameras with a sensitivity of 2000 frames/s useful for observing the dynamic deformations of the impact protection.
EXPERTISE, DESIGN CAPABILITY AND STRATEGIC VISION: STOMMPY'S R&D DEPARTMENT
Behind the success of the project to create the new crash test device for crash protectors is all the know-how of STOMMPY's R&D department, a department established eight years ago with the intention of dedicating a branch of the engineering department to the development of new innovative products and the continuous improvement of existing ones.
Today, the department is managed by a team of three designers coordinated by an Operations Manager, Eng. Paolo Desiderioscioli, and has several important invention patents to its credit, including the FIXA BLOCK SYSTEM - the universal anchoring system for any type of floor that guarantees its non-breakage, the IMPACT SAFETY BOLLARD with modular height, and the S.M.A.R.T. Safety Monitoring and Active Reporting Technology system - the first Impact Safety Bollard with IoT technology.
The other project of strategic importance in which the R&D department is involved is the development of the first industry standards to regulate impact protection in the industrial field. The standards are being studied by UNI, whose contribution of experience has been fundamental to the development of the work of the technical committee; a committee chaired by INAIL, reconfirming the growing interest of institutions in this sector.
Two documents are emerging from this project that will mark an important step forward in the regulation of the field in which STOMMPY operates: a technical specification that defines the testing and classification methodologies of impact protection, and a technical report that supports the end user in the correct choice of protection.
In this regard, it is important to note that the new crash test device signed STOMMPY already faithfully complies with the indications contained in the product classification technical specification under development at UNI, its design being contextual to the development of the standard.
PROJECTS OF EXCELLENCE ALSO COME ABOUT THROUGH COLLABORATIONS OF EXCELLENCE
Several realities among companies and institutions contributed to the success of this project, one above all the University of Modena and Reggio Emilia, each representing excellence in its field, from mechanical design to control electronics design, from management software development to mechanical and electrical wiring. All these realities have been wisely selected and coordinated by Eng. Desiderioscioli, who deserves credit for having been able to direct this large team by getting the best from each of its components.
According to Eng. Desiderioscioli himself, "The biggest challenge was to coordinate a project that was based on a standard that was still being defined and constantly changing, month after month. It was therefore necessary to develop and maintain a strategic overview of the two components, the normative and the operational, so that they were consistent with each other. This was not always an easy task, but it certainly increased the value of the project and created an important competitive advantage for STOMMPY's future."