With UNI Standard 11886, impact protectors become collective protective devices.
As of October 2022, for the first time industrial impact protections are included in a UNI standard, linked to DL 81/08 (Consolidated Law on Safety of Workers in Workplaces). As a member of UNI, STOMMPY played a key role in the development of the standard, putting its knowledge at the service of the body.
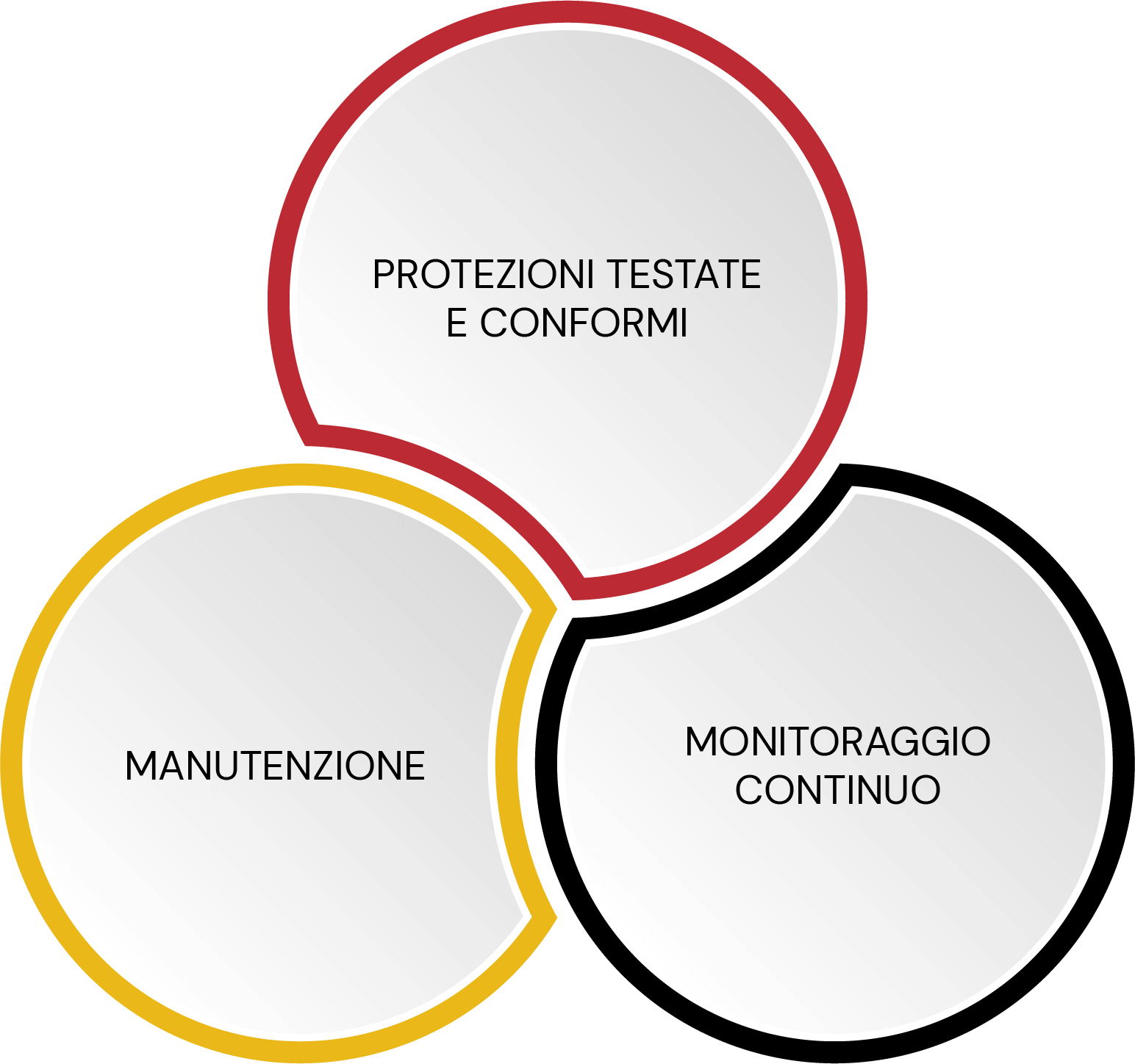
TESTED AND COMPLIANT PROTECTIONS
STOMMPY products are fully compliant with UNI Standards.
Each is accompanied by a detailed data sheet of the geometric performance characteristics as well as the results of the tests to which it was subjected.
.jpg)
Product data sheets.
The new UNI standard requires a more detailed and clear communication of the geometric and performance characteristics of the Impact Protectors by the Manufacturers, in line with the classification parameters indicated in the technical specification, in order to unify the information on the Impact Protectors provided by the Manufacturers with the parameters that the proper Impact Risk Assessment (DVR) will highlight in the processing.
The Data Sheets highlight:
- ENERGETIC CLASS of impact resistance for which protection has been tested and guaranteed;
- the stated WORK INGROUND;
- The SEVERITY INDEX (ASI) at impact;
- The URBENT SURFACE of each protection;
- The URGENT REGION of each protection.
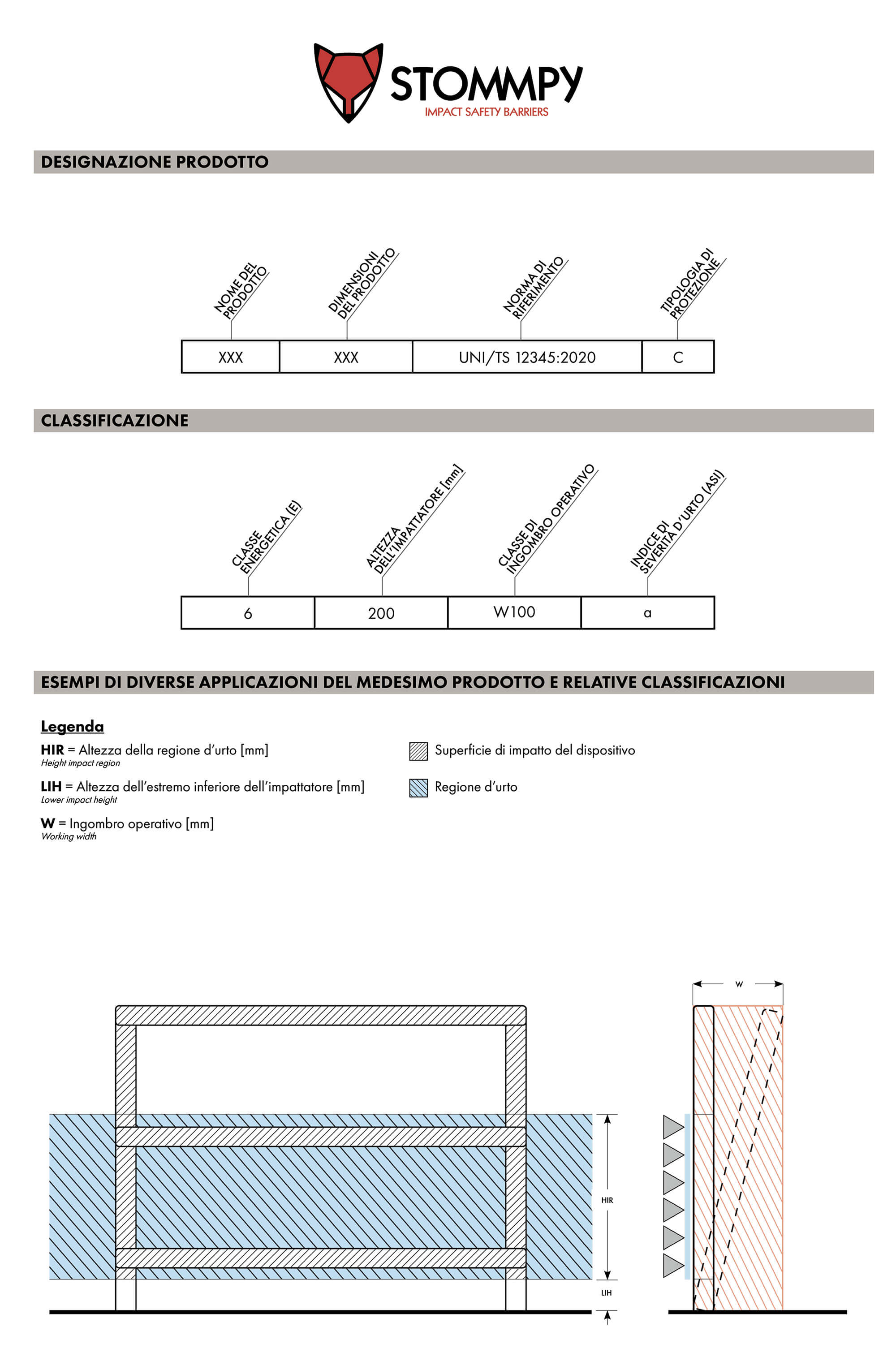
Crash Test STOMMPY: from the R&D department comes a unique crash protection testing machine.
STOMMPY's Research & Development Department has designed the first crash test machine, worldwide, that operates in a way that is fully compliant with the requirements of the UNI standard on Impact Protection in the Industrial Environment.
It is a slide system, an inclined plane on which, to simulate an impact against a protective device, three different mass values - 1,500, 4,000 and 6,000 kg - can be configured according to the UNI technical specification.
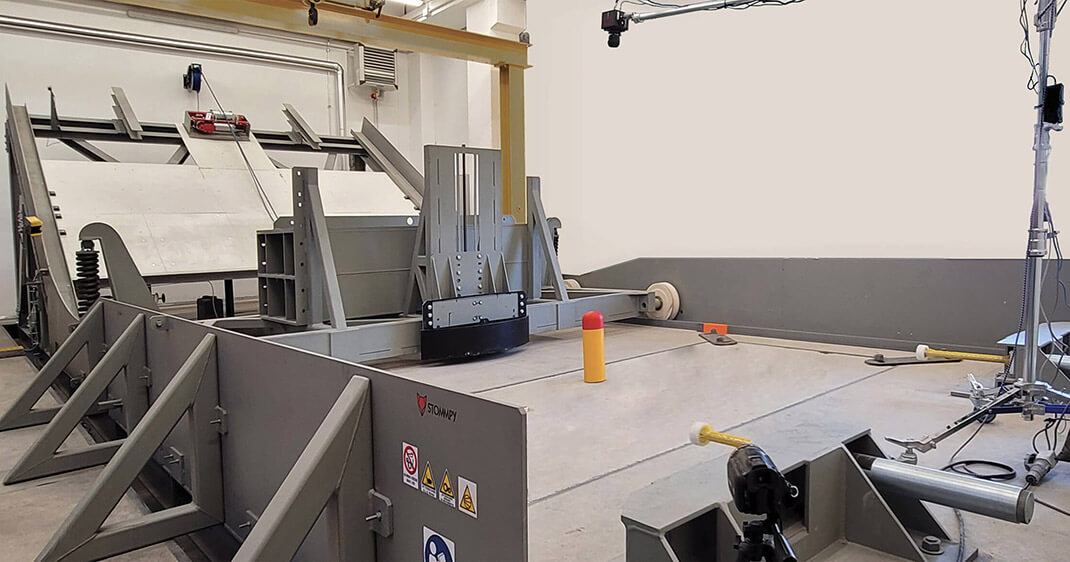
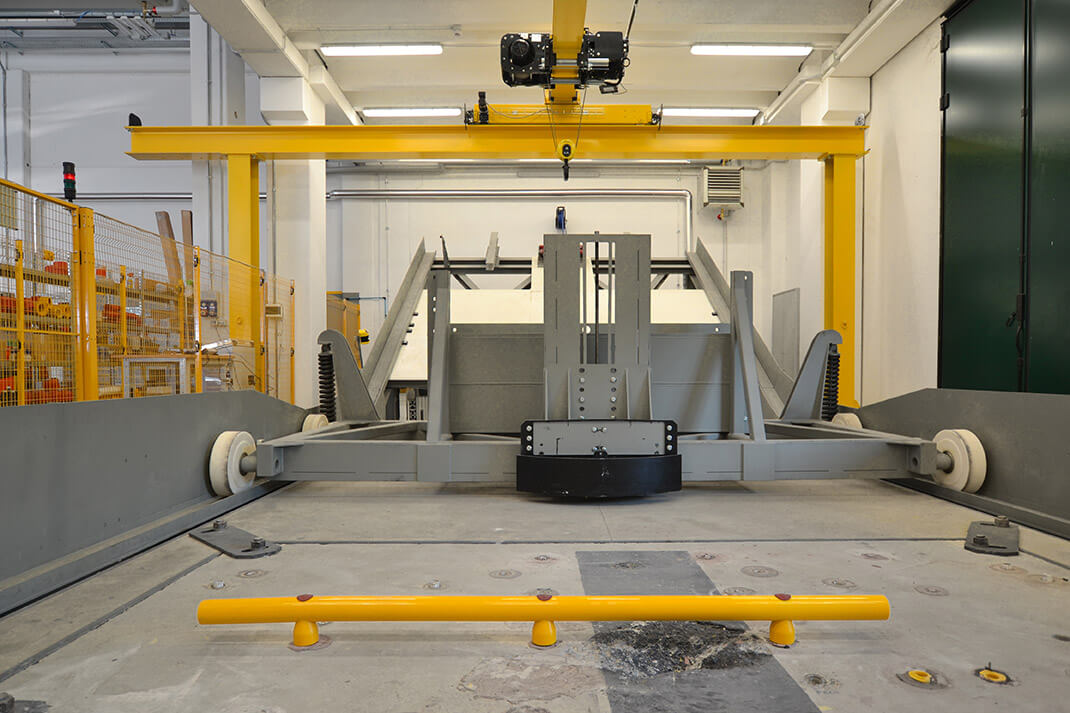
The machine has been appropriately oversized in its mechanical structure to be able to safely develop dynamic shocks up to the extraordinary value of 60,000 joules, well beyond the already considerable value of 50,000 joules of the maximum class of resistance provided for in the UNI technical specification;
The system is fully managed by a dedicated software, developed in collaboration with a specialized company according to the specifications and direct supervision of STOMMPY's R&D department.
MAINTENANCE
Scheduled maintenance system
STOMMPY products are designed and manufactured to last and to offer significant savings precisely because of this distinguishing feature. Through the STOMMPY scheduled maintenance system, in addition to obtaining the constant efficiency of all our products, it is possible to obtain an extended warranty period.
Contact us for more information.
Service for maintenance of guards, possibility of extending product and floor warranty up to 10 years to maintain compliance with UNI 11886 over time.
CONTINUOUS MONITORING
STOMMPY shock protection becomes "smart" thanks to innovative S.M.A.R.T. technology.
Inside (and outside) the plants, monitoring the efficiency of the Impact Safety Barriers is now exclusively entrusted to the visual check of the managers in charge. Result: too often, the damaged impact safety barriers remain in a condition of poor or event total lack of efficiency, for a short or a long time.
In the event, statistically high, that a forklift hits an already damaged Impact Safety protection, its definitive collapse could likely happen, increasing the risk of damages inside the company or causing injuries for workers.
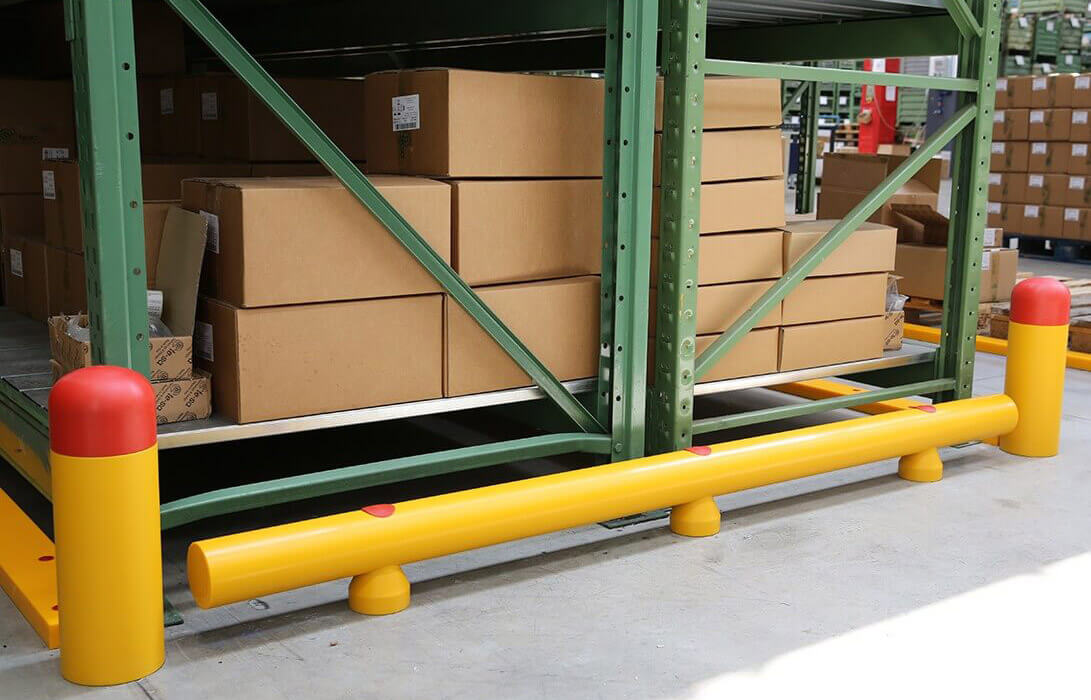
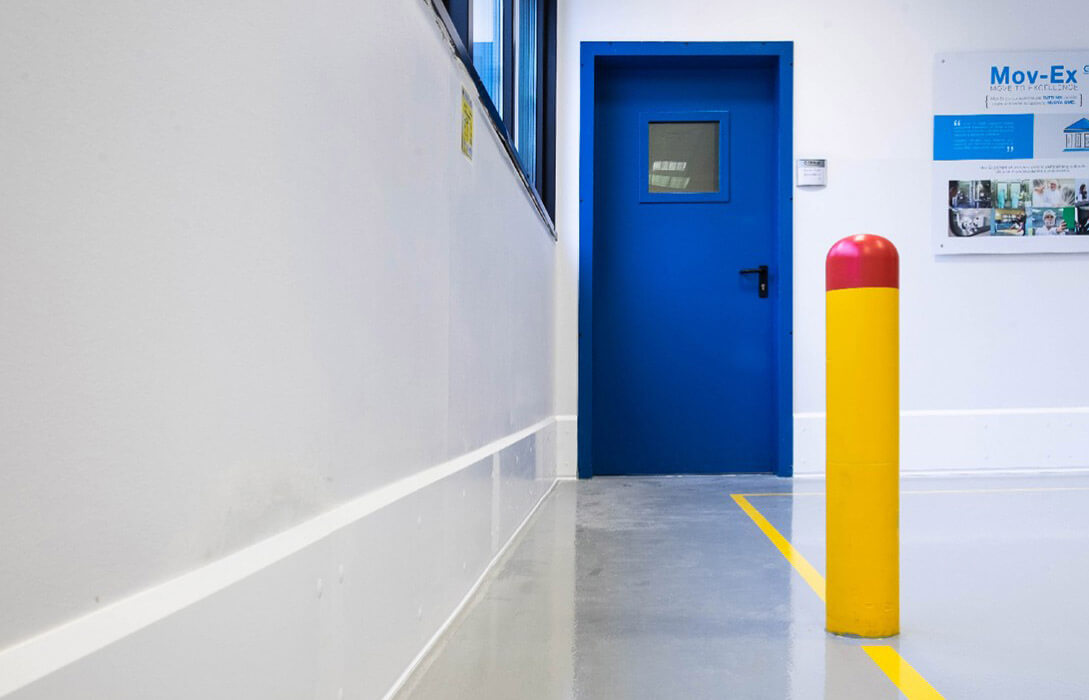
Thanks to the S.M.A.R.T. technology, STOMMPY transforms its Impact Safety Barriers, bringing them "on-line," and making them able to interact with the company managers in charge, communicating them in real-time any impact of a forklift against one of them, also indicating the degree of residual efficiency of the protection and the recommended action to be carried out in terms of maintenance.
Acomplete 4.0 safety system, therefore, realized while maintaining the performance characteristics of STOMMPY Shock Protectors, which are distinguished by their construction and anchoring materials, patented and certified according to the highest quality standards.
The full text of UNI Standard 11886 is available from the UNI STORE at these links:
UNI/TS 11886 - PART 1 is dedicated to manufacturers
Contact us for more information.
2022
THE REVOLUTION
UNI - Ente Nazionale Italiano di Unificazione e Normazione (Italian National Unification and Standardization Body), took up the request with much interest, forming a Working Group composed of a large and representative group of domestic and international manufacturers of impact protection and occupational safety representatives. In 2022, after three years of work, they created the first reference standard in Europe.
2017
THE EVOLUTION
In 2017, in order to bring clarity and ethics to a confused and deregulated market regarding Impact Protection in the industrial field, STOMMPY submitted a request to UNI to develop a specific standard to regulate the sector and fill the regulatory gap.
To do so, STOMMPY made itself available to share all of its technical experience, developed over twenty years of R&D on impact energy absorption and control techniques, collected in its DSP Guideline Safety Bump Devices; a document that STOMMPY created and disseminated to its customers.
2015
THE ORIGIN
In 2015, the need arose to develop technical standards on impact protection for industry to fill the regulatory gap in the industry.
Without them, manufacturers would have no baseline specification to adhere to in producing them, testing them, and communicating their performance in a way that is unambiguous and comparable by users.
Users would not have a guideline to follow in order to fully and correctly develop their Impact Risk Assessment Document in the company, they would not know what are the performance specifications to be considered for a correct choice and application of Impact Protection, now that the UNI Standard promotes and compares them to "Collective Safety Devices."